The challenges in designing high-performance aeronautical combustion systems have not changed signif- icantly over the years, but the increase of stringent regulations and the need to tackle rising fuel prices require new sophisticated analysis processes. To address this concern, the theme of this study was cast in
terms of the ability of improving the performances of advanced non-intrusive instrumentation in high- pressure turbulent reactive two-phase flows to enhance the combustion efficiency and reduction of pol- lutants of new innovative low-NOx injection systems fed with liquid kerosene. In the first part, a Lean
Premixed injection system designed for helicopter engines was first studied using the Particle Image Ve- locimetry (PIV), Phase Doppler Anemometry (PDA) and Planar laser-induced fluorescence (PLIF) of OH, kerosene vapor and NO. These diagnostics were applied individually or in combination for custom-made solutions for accessing to detailed information on the spatial distributions of velocity, droplets size, OH, kerosene and NO molar fractions in pressure conditions ranging from 0.4 to 1.8 MPa. Complementary large-Eddy simulations of these flames were performed using the PCM-FPI tabulated chemistry approach
in conjunction with a polydisperse Euler–Lagrangian approach. Comparison of simulations with experi- ments highlighted the importance of the size distribution of the droplets injected into the flow on the mutual predictions of the aerodynamic field, the structure of the flame and its anchorage point as well as the spatial distribution of the fuel and OH species. The second part of this work was aimed to study
the advantages and limitations of the chirped probe pulse femtosecond coherent anti-Stokes Raman scat- tering (CPP fs-CARS) diagnostic for performing time-series of single-shot temperature measurements on
an aircraft multi-point injection system developing two-phase flames under realistic pressure conditions.
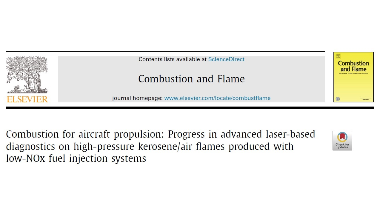